The Monki line-up consists of just two garments – a grey hoodie and track pants – made using the so-called Green Machine technology. But it represents a tipping point on the fashion industry's path to a circular model.
The majority of clothes produced today are made of cotton and polyester blend fabrics. And until now there has been no commercial method to fully recycle these garments into new ones.
Using a closed loop of just water, heat and biodegradable green chemicals to separate the fibres, the new hydrothermal system is for the first time moving from trial to products. Next it will be scaled up for commercial production at Indonesian manufacturing giant PT Kahatex, before the technology will be made available under license for the rest of the industry to use.
Developed by HKRITA (The Hong Kong Research Institute of Textiles and Apparel), the environmentally friendly process is “like a pressure boiler that you might have in your kitchen,” explains Erik Bang, innovation lead at non-profit H&M Foundation, the research collaborator.
“What we're talking about here is one puzzle piece of closing the loop. But to get the Green Machine technology out from a laboratory and into a commercial line, that is a huge step.” - Jenny Fagerlyn, Monki's global sustainability director
The real advantage with the Green Machine, he adds, “is that we're not breaking down the polyester. We're recovering it in fibre form and with fibre quality, so we can re-spin it into a yarn right away." What’s more, the polyester fibres can be recycled over and over again without loss of quality.
This is what will happen at PT Kahatex, one of the largest textile and clothing enterprises in Southeast Asia. Not only has the manufacturer made Monki's new capsule collection, but it is also due to take delivery of the first Green Machine and will play a key role in helping to optimise the hydrothermal separation process on a larger scale.
The system is currently configured to separate about a ton and a half per day of blended fibre materials. And because it's modular, it's a simple case of adding more units – either independently or in coordination – to build capacity.
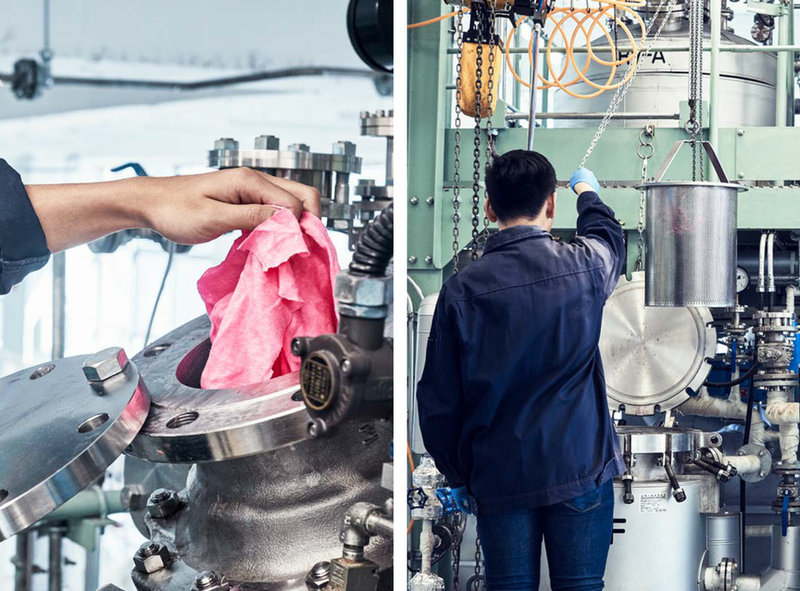
Numerous challenges
The hydrothermal technology is the culmination of research that began in 2016, and will be an important step in preventing millions of tons of textile waste ending up either discarded in landfills, or downcycled into insulation and other low value applications each year.
"Because polyester is so cheap, you need to have a very competitive process to enable recycled polyester to compete with virgin polyester on price,” Bang says. “This is why the Green Machine is modular, why we don't break down the polyester, and why it's a closed loop system so we recover the heat, water and chemicals."
In contrast, the current process of using PET plastic bottles as the raw material for recycled polyester is not only costly but requires specialist equipment and "a big, super-expensive factory" to convert the material back to its original monomer feedstocks before it can be reconstructed in fibre form. Until now, there has been no way to recycle these fibres at scale.
Bang also points to the logistical challenge of "the stuff we want to recycle sitting with the consumer at the end of life, but we need to get it back to be able to recycle it."
Game-changing potential
It's here that he believes the new technology has more game-changing potential.
"Recycling will unlock a number of other levers when it comes to how the fashion industry is set up, its dynamics and its structure. With the Green Machine we can recycle where the waste is [rather than] shipping it back along the supply chain to recycle it on the other side of the planet.
"So I think we will see regionalised and localised recycling, as well as garment collecting, within trade blocs of the EU, the US and others. And that will enable a whole new set of localised production, on demand, and closer to the customer.
"This will take away the need for inventory and pre-planning of collections: you can run the cycle much closer to actual demand and that, in itself, will reduce the waste of overproduction and loss in the supply chain."

Huge step
Jenny Fagerlyn, Monki's global sustainability director, emphasises that the Green Machine is just one solution to the bigger goal of a circular fashion system that can recycle and reuse the endless variety and composition of textiles.
"What we're talking about here is one puzzle piece of closing the loop. There are multiple processes and discussions and systems that need to be in place – but to get the Green Machine technology out from a laboratory and into a commercial line, that is a huge step.
"My belief is that each industry should close their own loop and deal with their own waste into the loop. And I think that is how you build a circular economy in the future – not to try to bend a linear model into a curved one, like using PET bottles for recycled polyester.
"As brands it's our responsibility to invest in platforms and services that ensure the product has a long life."
The need for change has also been highlighted this year more than ever before. "From trade wars to Covid, it has never been more clear how vulnerable the supply chain is. We need to be much more diversified,” Fagerlyn adds.
BACK TO TOP