China's top leadership has made pollution control one of the "three tough battles" that China must win to build a well-off and sustainable economy and society by 2020. And the introduction of an environmental protection tax in China just over a year ago is helping to curb polluting textile manufacturers.
However, it has also pushed up the price of fabrics produced in the country – thereby increasing costs for Chinese clothing manufacturers – experts have told just-style.
The tax, introduced in January 2018, provides an incentive to cut pollution because it is based on the actual amount of discharge of pollutants into water, air, as solid waste, and as noise. The previous system simply applied the same fee on all factories regardless of their actual discharge.
The textile and clothing sector is particularly exposed, since according to China's ministry of environmental protection it is traditionally the third-largest source of industrial wastewater in the country.
“China-based finishers have also been investing in more expensive digital printing to colour fabrics and sometimes packaging, which reduces the amount of water used compared to traditional dyeing processes.”
"In the past year, smaller textile enterprises have found it challenging to find the capital required to upgrade their equipment, and have either closed or are facing financial challenges," says Kerstin Brolsma, a business analyst with China Market Research Group (CMR), in Shanghai.
Sofya Bakhta, a marketing strategy analyst with Daxue Consulting, also based in Shanghai, notes that another cost for manufacturers has been to create and check chemical inventories so they can demonstrate to buyers that they comply with a restricted substances list developed by the ZDHC Roadmap to Zero Programme.
China-based finishers have also been investing in more expensive digital printing to colour fabrics and sometimes packaging, which reduces the amount of water used compared to traditional dyeing processes.
Stricter monitoring of textile factories is partly driven by a Water Pollution Prevention and Control Law. This was implemented concurrently with the Environmental Protection Tax and entails, among other measures, that officials will lose promotion opportunities if they are found to be lax in their enforcement of these controls.
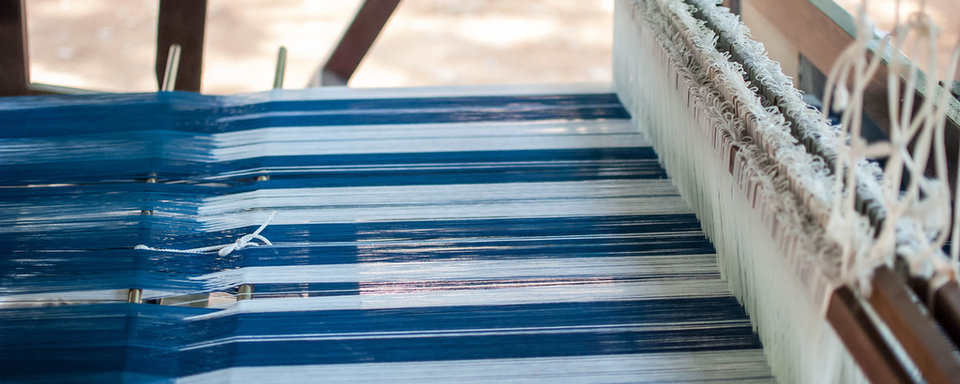
Green factories boost Bangladesh
The Rana Plaza tragedy pushed Bangladesh's US$30bn clothing industry into making health and safety improvements to reassure brands they would not be tarnished by similar disasters – and now the industry is going a step further by seeking to establish a reputation for environmental excellence.
One case in point is Remi Holdings, a textile maker working from the Adamjee Export Processing Zone in Narayanganj, near Dhaka.
Remi, an arm of the Bangladesh-based Bitopi Group, which has holdings in garments and advertising, operates a platinum-rated green factory scoring 97 out of 110 points on the US Green Building Council (USGBC) certification scheme. The group's Tarasima Apparels, based at Manikganj in Dhaka, also has a USGBC platinum rating.
To secure this, Remi has spent US$20m on improvements such as waste water controls (half the emissions compared to standard plants), ensuring 35% of lighting is energy-efficient, 75% of the premises has natural light and 9% of energy comes from onsite solar power.
The two-year-old factory turns over US$32m annually, making more than half a million bottoms for top retailers such as Hennes & Mauritz (H&M), Primark, Target, Benetton and Promod.
“Bitopi is part of a larger story that has seen some 67 garment factories in Bangladesh achieve LEED certification that evaluates location, sustainable sites, water efficiency, energy, indoor environment and innovation.”
Bitopi managing director Miran Ali says the cost of establishing such green factories is 25% higher than for a conventional unit, but there are clear benefits. In particular, orders have been placed by buyers who want to market clothing as sustainable as possible.
Environmentally-managed clothing factories have an edge in the outsourcing market, something Ali insists "differentiates us from Vietnam, Cambodia and Indonesia," Bangladesh's major regional rivals. Manufacturers building green credentials will benefit "in the long-term," he adds.
And they need to compete, given most new garment factories in Bangladesh have at least adopted USGC's LEED (Leadership in Energy and Environmental Design) certification. "Entrepreneurs have realised this is the only way forward," says Ali.
He also hopes global buyers will recognise the national industry as one that is developing an environmentally-sustainable apparel sector with an international reputation for good practice.
Bitopi is part of a larger story that has seen some 67 garment factories in Bangladesh achieve LEED certification that evaluates location, sustainable sites, water efficiency, energy, indoor environment and innovation.
As of June last year, there were eight LEED platinum certified plants in Bangladesh, according to a study commissioned by the UK's Department for International Development (DfID). Some 280 Bangladesh factories are in the process of getting LEED-certified, according to the report.
BACK TO TOP