Cover Story
The fashion supply chain’s technology transformation
Hannah Abdulla explores how technology has influenced fashion production and how it will continue to do so in the years to come.
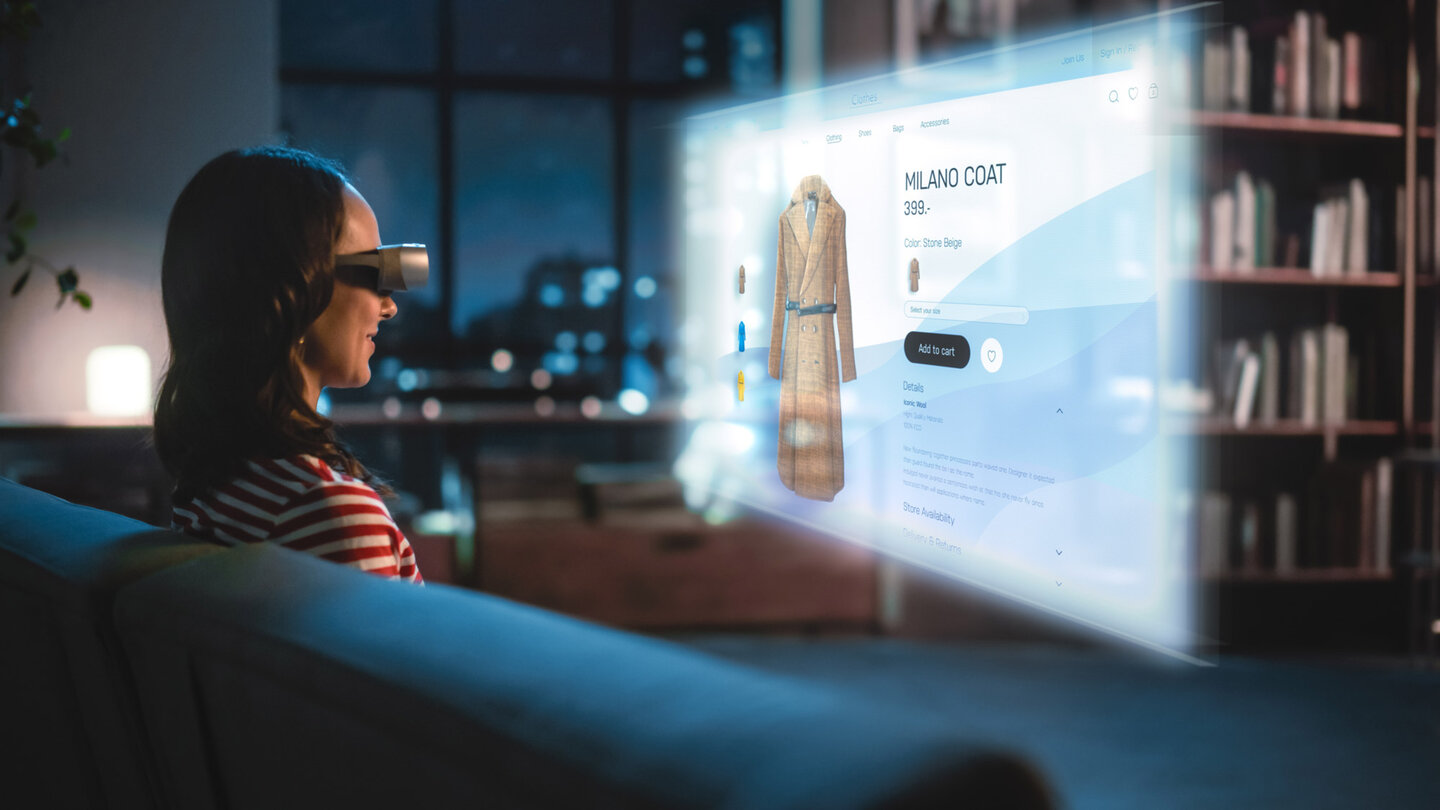
There can only be positives in trying out new technological capabilities. Credit: Gorodenkoff / Shutterstock
The constant evolution of technology has dramatically changed the way the fashion supply chain operates. Moving from manual processes to semi-automated and fully automated has driven efficiencies and improved sustainability.
But as technology becomes more sophisticated and we witness robotics, artificial intelligence and Gen AI entering the mainstream, it begs the question: how much tech is too much and what will be the wider impact on the fashion supply chain and the people behind it?
Embracing the AI revolution
AI will have a huge influence on the future of fashion supply chains, according to industry experts.
Lever Style has a goal to transform the entire pre-production stage (from order placement to production allocation) from being a series of unstandardised and human-driven processes into a system-driven coordinated flow.
It is now working on developing an AI apparel production platform that matches apparel brands and orders to the most optimal producers in real time.
SunTekstil, a Turkish garment manufacturer, has introduced Refabric, a new AI-powered design platform that transforms ideas into designs within minutes and creates collections aligned with trends, says chairperson of the board Elvan Ünlütürk, adding AI is something SunTekstil has been slowly investing in since 2020.
“We only see this increasing at pace due to the improvements we are making across our whole supply chain.”
What’s the catch?
MAS Holdings’ chief digital officer Steve Dodd says if businesses have a clear approach on how to experiment, clear entry and exit criteria, clear use cases and expected outcomes, and a fixed time, there can only be positives in trying out new capabilities.
“It's important to experiment in the right way. We need to test the theory rapidly, prove there is a value that can be unlocked, then deploy at scale. Too often we see organisations experimenting for months, then failing to find a use case that can deliver a return, or even simply losing focus of what they were setting out to do.”
PDS Limited’s Group CEO Sanjay Jain agrees: “Any new integration within an organisation comes with its set of challenges, from legacy system compatibility to workforce upskilling and data security. The rapid pace of technological evolution also brings risks, and without effective change management, organisations can struggle to adapt. Without a structured approach, resistance to change can lead to inefficiencies, disruptions, and missed opportunities.”
What other technologies are garment makers and brands leveraging?
AI is the buzzword across the industry, however the fashion sector still relies on tried and tested technologies.
PDS is exploring blockchain and IoT solutions to improve supply chain transparency and traceability. It also leverages AP ERP, AI-driven analytics, and its proprietary digital collaboration platform, WEAVE (Web Enabled Application for Vendor Management), to enhance visibility and optimise operations across 22+ countries.
Sun Tekstil uses several pieces of technology from robotic process automation for its order systems and 3D for its fitting and pattern making.
Dodd says MAS leverages many “off the shelf platforms” and that its business is reliant on multiple technologies.
“It is critical in today’s world, to use technology that is best in class for the core functional areas of one's business. As a manufacturer, that means using technologies that help to develop, plan and make products is key. The days of a single platform that can do everything is gone, now we need multiple tools with seamless integration to be efficient and agile as a business.”
How will tech impact the fashion sector over the next 5-10 years?
Lever Style is keen to position itself as a fashion production platform that matches fashion brands and orders to the most optimal producers in real time.
“With this platformisation, brands will benefit from unmatched production versatility and factory choices, while factories will tap into a wide range of brands and orders with minimal customer servicing cost and effort. Imagine a "ride-hailing" platform for garment production, that optimises apparel production on an order-by-order basis. Whilst this is a paradigm shift in business model, technology and AI will play vital roles in this transformation,” says Lever Style’s CEO William Tan.
Jain believes technology will continue to simplify and transform the way fashion supply chains operate.
He says: “Future innovations like AI-powered production planning and smart factories, will enable nearshoring, accelerate lead times, and drive data-driven sustainability — making fashion sourcing more ethical and efficient.”
Dodd agrees that manufacturing and product design will look very different to the way they do today.
He explains: “The challenge as we see it, lies with a move away from traditional, manual product creation to digital. The technology is available, but adoption by most apparel brands is very low, and in many cases it is brands who drive the product development process. Manufacturing is a huge area of opportunity, there are multiple aspects of product creation that can be improved through the use of robotics, computer vision and machine learning.”
Caption. Credit:
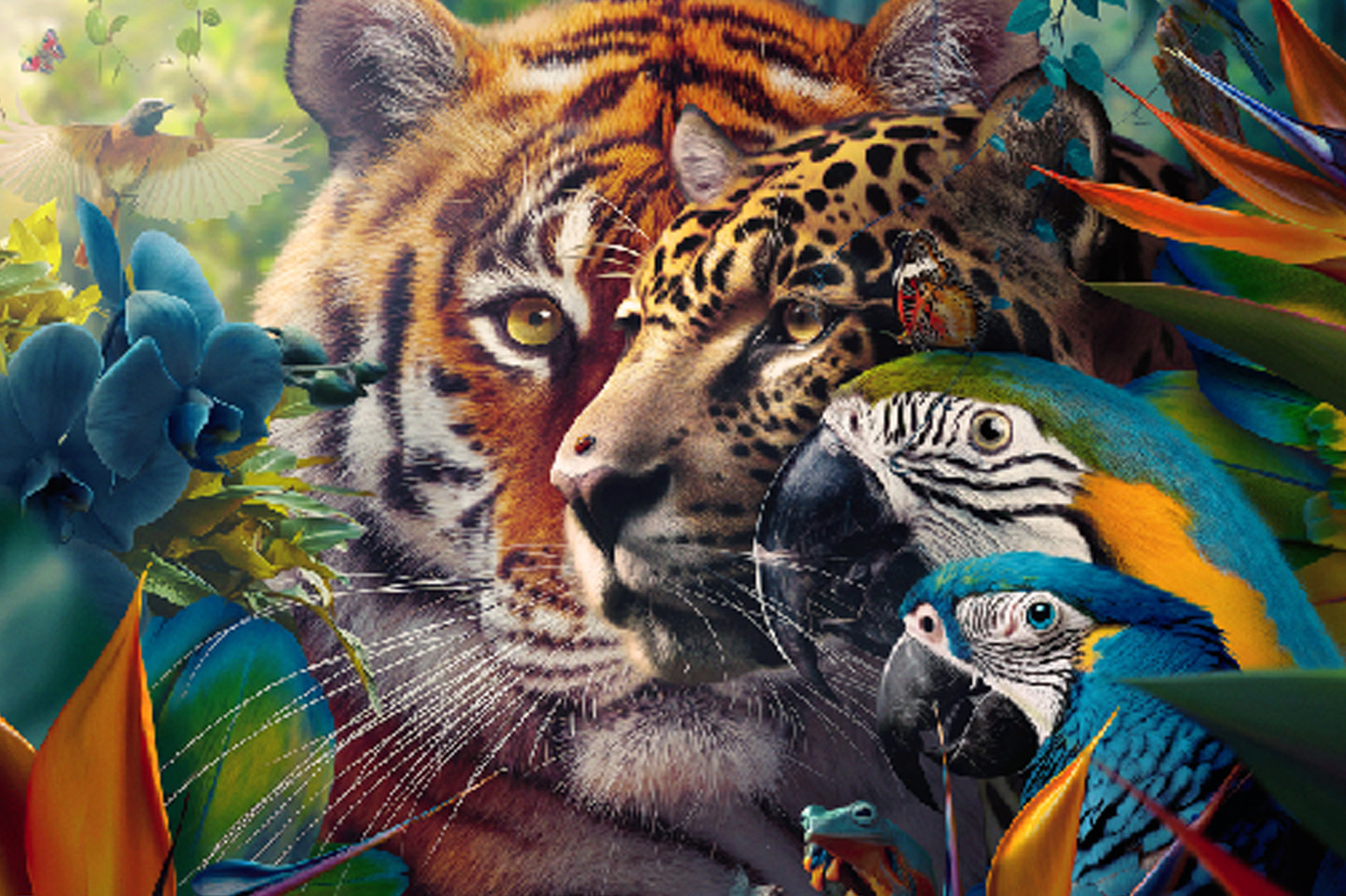
Caption. Credit:
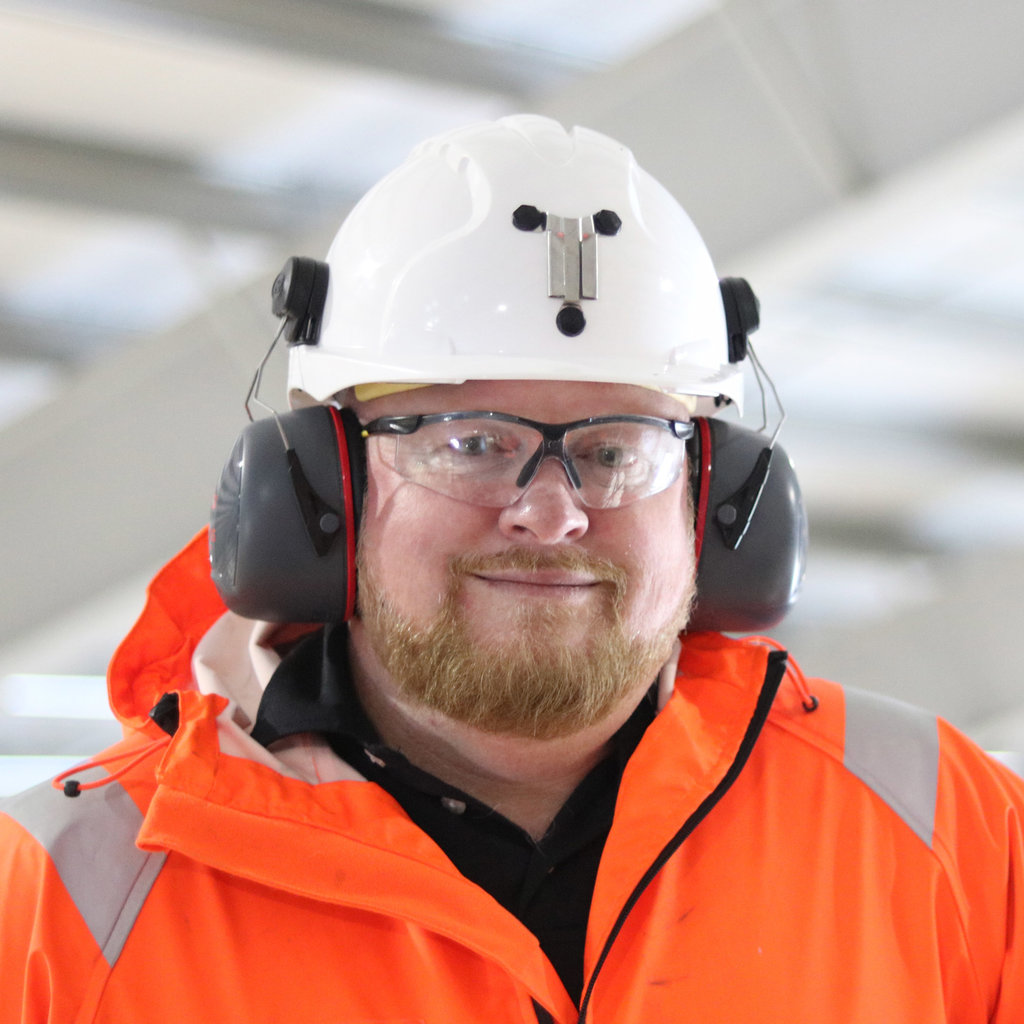
Phillip Day. Credit: Scotgold Resources
The mine’s orebodies are also particularly attractive for potential future investments, with phosphate deposits containing up to 70% rare earth oxides. Indeed, in August 2018, Lynas announced a 70% increase in the mine’s mineral resources and a 60% increase in ore reserves. This pushed the total life of the mine beyond 25 years, making this a reliable long-term project.
The mine’s concentrator can produce around 240,000 tonnes of ore, including around 26,500 tonnes of rare earth oxides. As mining processes improve and the facility begins to push towards this output maximum, this could prove to be a source of rare earths on a much larger scale than many of the high-potential, yet unproven, exploration-stage projects in the country.
While China’s rare earth production remains orders of magnitude greater than Australia’s, large-scale and well-established projects such as the Mountt Weld facility could be Australia’s best chance to threaten Chinese rare earth production on a large scale.
The mine’s concentrator can produce around 240,000 tonnes of ore, including around 26,500 tonnes of rare earth oxides. As mining processes improve and the facility begins to push towards this output maximum, this could prove to be a source of rare earths on a much larger scale than many of the high-potential, yet unproven, exploration-stage projects in the country.
While China’s rare earth production remains orders of magnitude greater than Australia’s, large-scale and well-established projects such as the Mountt Weld facility could be Australia’s best chance to threaten Chinese rare earth production on a large scale.
Total annual production
The mine’s concentrator can produce around 240,000 tonnes of ore, including around 26,500 tonnes of rare earth oxides.
Gavin John Lockyer, CEO of Arafura Resources
Australia could be one of the main beneficiaries of this dramatic increase in demand, where private companies and local governments alike are eager to expand the country’s nascent rare earths production. In 2021, Australia produced the fourth-most rare earths in the world. It’s total annual production of 19,958 tonnes remains significantly less than the mammoth 152,407 tonnes produced by China, but a dramatic improvement over the 1,995 tonnes produced domestically in 2011.
The dominance of China in the rare earths space has also encouraged other countries, notably the US, to look further afield for rare earth deposits to diversify their supply of the increasingly vital minerals. With the US eager to ringfence rare earth production within its allies as part of the Inflation Reduction Act, including potentially allowing the Department of Defense to invest in Australian rare earths, there could be an unexpected windfall for Australian rare earths producers.